The quality of the CAN node will bring a large security risk to the CAN bus network. Therefore, the consistency test of the CAN node is particularly important. This paper will discuss the input voltage threshold test of the CAN node.
CAN conformance testing is mainly divided into three parts: physical layer, link layer and application layer. In the CAN network, each node follows the CAN conformance test as an important prerequisite for ensuring stable operation of the bus. In the physical layer, the CAN bus design specification has strict regulations on the input voltage threshold of the CAN node. If the input voltage threshold of the node does not meet the specifications, the abnormal working state is likely to occur after the field networking, and communication occurs between the nodes. Fault, so the input voltage threshold test is also an important part of the CAN physical layer conformance test.
First, the test standard
Each manufacturer must perform the input voltage threshold test of the CAN node before the product is put into use. Generally, the ISO 11898-2 input voltage threshold standard is adopted. The specific requirements are shown in Table 1.
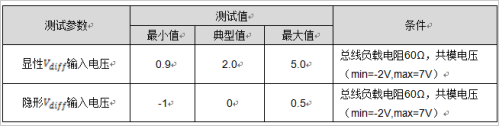
Table 1 ISO 11898-2 Input Voltage Threshold Standard
Note: For details of the input voltage threshold standard, refer to Table 4 (DC parameters for recessive output of CAN node) and Table 5 (DC parameters for dominant output of CAN node) and related parts in IOS 11898-2-2003.
Second, the test principle and steps
1. Implicit input voltage test
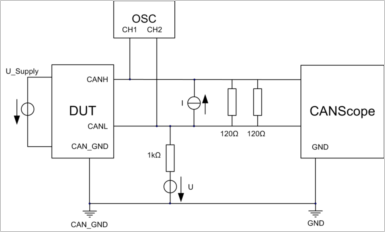
Figure 1 Stealth input voltage test principle
Under the bus load and common mode voltage conditions shown in Table 1, the implicit input voltage threshold test is performed according to the test principle of Figure 1:
Use CANScop e-Pro to monitor CAN bus message frames, and the DUT is in the state of sending messages;
Adjusting the voltage of the CANH idle time on the U-monitoring oscilloscope is -2V and 6.5V, respectively, and adjusting the current source I to make Vdiff reach the upper limit of 0.5V;
Note: For the accuracy of the results, repeat the above steps for 10 consecutive tests and record the results of each test.
Conclusion: At ≤0.5V, if the DTU can send a message normally, the invisible input voltage test passes.
2. Dominant input voltage test:
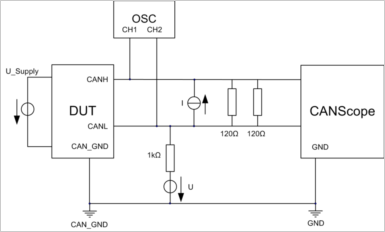
Figure 2 Principle of dominant input voltage test
Under the bus load and common mode voltage conditions shown in Table 1, the dominant input voltage threshold test is performed according to the test principle of Figure 2:
Use CANScope-Pro to monitor CAN bus message frames, and the DUT is in the state of sending messages;
Adjust the voltage of the CANL idle time on the U-monitoring oscilloscope to -2V or 6.1V respectively. Adjust the current source I to make the Vdiff step-by-step 0.1V, and then adjust from the implicit input voltage upper limit of 0.5V to the display. The lower limit of the input voltage is 0.9V.
Note: For the accuracy of the results, repeat the above steps for 10 consecutive tests and record the results of each test.
Conclusion: In both cases, when the dominant input voltage limit is 0.5V, the DUT should still be able to send CAN message frames. If the dominant input voltage limit reaches 0.9V, if the DTU stops the CAN message. The transmission of the frame passes the dominant input voltage test.
Third, CANDT conformance test system
In order to improve test efficiency, save labor costs, improve test accuracy, and avoid manual measurement of statistical errors, ZLG Zhiyuan Electronics has launched a CAN conformance test system. CANDT is based on the ISO11898 standard and is built around the domestic mainstream new energy host factory CAN bus test. The standard is the main basis, and the test function satisfies the testing requirements of the physical layer, the link layer, and the application layer.
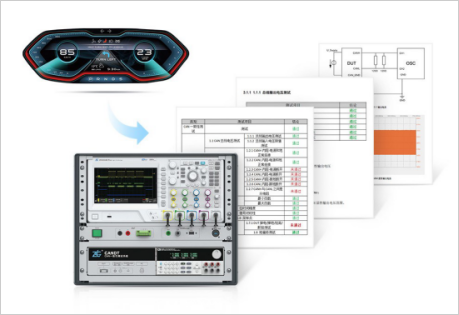
By connecting the car or single-node components to the CAN conformance test system, the CAN bus physical layer, link layer and other tests can be automated, and the test report can be automatically exported, which can be used as the basis for the host factory. After the CANDT conformance test, for the problem that the test report fails in the test report, CANScope can be used for fault location and troubleshooting to speed up the stable development of the CAN bus.

3D Printing Auto Production Line
3D Printing Auto Production Line,3D Printed Solid Sand Mold,Resin Sand Molds For Casting,Small Build Volume 3D Printer
Guangdong Fenghua Zhuoli Technology Co., Ltd , https://www.fhzl3d-print.com